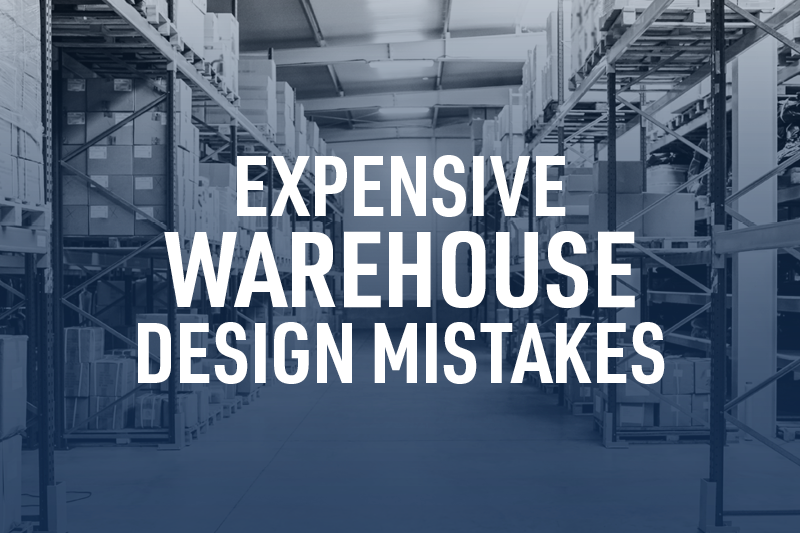
Imagine your pre-work routine. If you’re a warehouse or distribution center manager, I bet it’s finely-tuned to be as efficient as possible. You probably don’t:
- Brew your coffee in the kitchen but keep your coffee mugs in the garage
- Store your socks in a box on the top shelf of your closet
- Keep your clean shirts under a pile of dirty shirts
No one would organize their home this way because you’d waste an insane amount of time accessing essential items. Unfortunately, many local distribution centers and warehouse waste time (and money) every day because of inefficient layouts.
In many cases, bad warehouse design is caused by inertia. Products or product velocity changes, but the layout remains the same because there’s never a good time to drop everything, assess and reorganize.
But the truth is, optimizing your warehouse layout is one of the best investments you can make (especially when you can get a free warehouse design consultation from The Lilly Company). Read on to learn about the most common warehouse space planning mistakes and warehouse building design best practices.
An Optimized Warehouse Is a Competitive Advantage
According to MHI’s annual industry report, customer demands for lower costs and faster response times are among the top five challenges faced by supply chain managers.
An optimized warehouse layout allows you to improve efficiency, speed up fulfillment time and lower costs. In short: it gives you a competitive edge.
Changing your warehouse design doesn’t have to mean starting over from scratch. It could simply mean moving popular items closer to the loading dock or staging area, or maximizing your existing space by using taller racks or partially converting to narrow aisles.
We get it, the last thing you want to do is disrupt your business. That’s why we offer free warehouse design consultations. After learning about your operation, our warehouse expert will suggest different ways to optimize your current space.
Our experts can help you save time, money and avoid common warehouse design mistakes such as:
- Not collecting enough information about product cube velocity
- Forgetting to check the fire code for product-specific sprinkler needs
- Failing to maximize vertical space
- Converting to aisles too narrow for existing equipment
- Creating a system that can’t adjust to growth, product or velocity changes
- Choosing the wrong racking system for FIFO, LILO, ECT, etc.
- Using a supplier with insufficient layout and storage knowledge
- Prioritizing upfront price versus long-term profitability
Free Warehouse Design Consultation: What to Expect
During our free consultation, we’ll take the time to get to know your business. Really. We want to provide cost-effective ideas tailored to your business, not a cookie-cutter solution.
We’ll gather information about:
- The size of your space, including ceiling height and any obstructions (such as columns)
- The material handling equipment you own
- Product width, length, height and max weight
- Product cube velocity
After the free assessment, we’ll provide one or more warehouse designs for you to choose from. If you decide to move forward, here’s what happens next:
- Decide on layout type (or types) and storage to be used
- Client reviews drawing layout, we make changes until approved
- Discuss project timeline and desired in-service date
- We send the design for seismic calculations
- Client reviews final quote and drawings
- Client generates PO
- We order materials from manufacturers
- Material arrives and is unloaded
- Installation begins with levels and spacing approved again by client
- Installation complete
- Fire dept. inspection and building inspection.
- Customer walk thru and sign off
- Project completed
Professional Warehouse Building Designs in the Mid-South
Warehouse optimization and space planning is one of the best investments you can make for both the short and long term. Unfortunately, many operations aren’t as profitable or competitive as they could be because of an outdated layout.
Maximizing the efficiency and profitability of your operation costs only a few moments of your time. Contact a warehouse design expert at The Lilly Company online or by phone 844-LILLYCO (1-844-545-5926) with any questions you have, or visit a location near you. We have 13 locations across the Mid-South.
Arkansas - Jonesboro
Alabama - Birmingham, Dothan, Irondale, Madison, Mobile, and Montgomery
Mississippi - Tupelo and Richland
Tennessee - Jackson, Kingsport, Knoxville, and Memphis
Further Reading:
Ladder Safety: How to Avoid Lawsuits and OSHA Citations
5 Simple Ways To Improve Loading Dock Safety & Efficiency
Bollards, Guardrails and 3 More Money-Saving Warehouse Safety Products
Posts by Tag
- Forklift (61)
- Forklift Service (19)
- Electric Forklifts (16)
- Forklift Safety (14)
- Forklift Attachments (12)
- Toyota Forklifts (12)
- Warehouse Planning (10)
- Parts (9)
- Warehouse Automation (8)
- Clark Forklifts (7)
- Loading Docks (7)
- Material Handling Education (7)
- Pallet Racking (7)
- Customer Solutions (6)
- Forklift Batteries (6)
- Forklift Rental (6)
- Purchasing Options (6)
- Aerial Equipment (5)
- Heavy Equipment (5)
- Forklift Accessories (4)
- Forklift Fleet Management (4)
- Forklift Tires (4)
- Forklift Training (4)
- Products (4)
- Utility Vehicles (4)
- Yard Spotter Trucks (4)
- Linde (3)
- Pallet Jacks (3)
- Specialty Forklifts (3)
- Used Equipment (3)
- IC Forklifts (2)
- Manitou (2)
- Warehouse Doors (2)
- COMBiLift (1)
- Custom Shop (1)
- Forklift Brakes (1)
- Forklift Warranty (1)
- Gehl (1)
- Komatsu (1)
- Product Review (1)
- Recruitment (1)