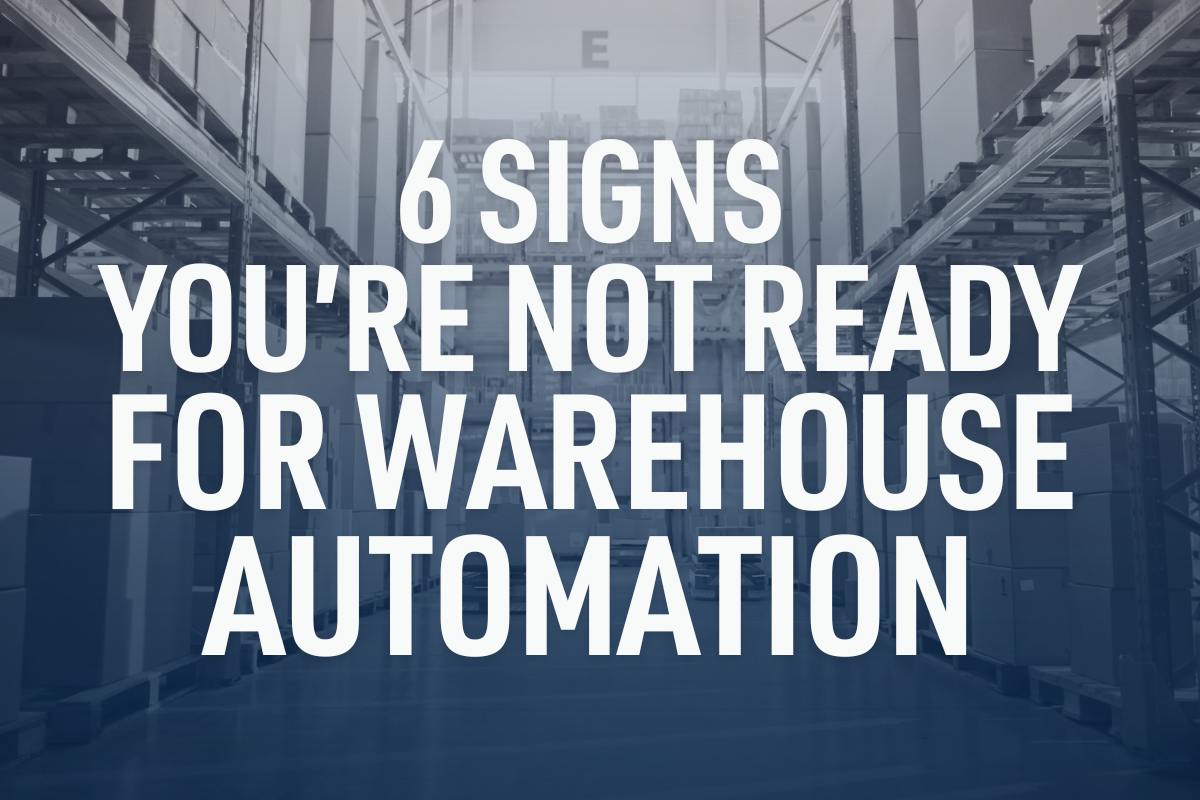
You might have heard statistics like 25% of warehouses worldwide use automation or 60% of warehouses plan to increase their automation spending. If so, you might be wondering if you're missing out. It's true that automation has the power to revolutionize most warehouses, but there are cases when it isn't the best choice. So, if you're wondering about automation, read on to discover the six signs you aren't ready to automate.
What Is Warehouse Automation?
Warehouse automation is a term that encompasses a variety of technologies that accomplish warehouse tasks with little or no human intervention. Some of these technologies, like conveyor systems, have been in use for some time. Others, like automated forklifts, are emerging technologies. Likewise, warehouse automation refers to both hardware and software, with even some warehouse management software (WMS) falling into this category.
Automation offers a variety of benefits, including faster order processing, improved inventory management, a safer facility, and labor savings. However, automation isn't for everyone. Below are six signs your facility might not be ready to automate.
1. Your Order Volume Is Low
One of the primary benefits of automation is the ability to do more with less. Many warehouse automation solutions like automated guided vehicles (AGVs) focus on accomplishing repetitive tasks like transporting material throughout your facility. By passing this tedious, time-consuming labor off to a machine, you free up your staff to focus on the jobs where they can add value. This provides a crucial productivity boost, especially for businesses that experience seasonal surges.
However, if your order volume is consistently low, AGVs might not be your best choice. While automation would undoubtedly free up your team members for other projects, it’s wasted if you don’t have the order volume to justify the expense. Of course, if your order volume is low because your process is labor intensive, automation could free up time for your staff to increase sales volume.
2. You’re Warehouse Is Already Safe Enough
Warehouses can be dangerous places, and working around moving equipment can be hazardous to pedestrians. That's why most modern AGVs feature collision avoidance software. For example, the Tennant T7AMR Robotic Floor Scrubber is an autonomous industrial cleaning machine that uses natural features navigation to negotiate even the busiest warehouses. Its detection software is intelligent enough to automatically stop for obstructions. It can even change paths to navigate around stationary obstacles.
However, if your warehouse has few staff, limited heavy machinery, and infrequent pedestrian traffic, autonomous safety features are less vital because the statistical risk of an accident is much lower than in larger facilities.
3. Your Available Storage Space Exceeds Your Inventory
Another significant advantage of automation is optimizing your storage capacity. Automated storage, like cube storage, ensures you don't waste an inch of available space. In these systems, products live in a dense matrix of bins. When an operator wants to retrieve a particular product, they input the order, and a robot cycles the bins until it retrieves the requested item. It then delivers the bin to the picking station.
Storage density isn't a primary concern if your warehouse has more than enough space to store your inventory. In that case, traditional racking and shelving options are more than sufficient for your storage needs. Likewise, traditional solutions will also be more cost-effective for you.
4. You’re Still Figuring Out Your Process
Automation is incredibly customizable and modular. Autonomous equipment like Toyota's automated tow tractor is programmable for just about any transport process. However, even smart machines have to be told what to do. Even the most advanced automation solutions will provide little benefit if you haven't yet standardized a process for your facility. Before you consider automating, you'll want to optimize and lock down a consistent process that your automation can follow. That doesn't mean your process can't continue to evolve even after adopting automation. Still, the fewer changes you make, the less you'll need to modify your autonomous units, and the more benefit you'll get from automation.
5. You’re Not Worried About Improving Inventory Inaccuracy
For high-throughput facilities, even a 1% pick error rate can mean serious revenue loss. Automated storage systems like vertical lift modules help eliminate those errors. These units store products vertically in densely organized bins. When a product is requested, a robotic shuttle selects the appropriate bin and delivers it to the floor-level picking station. This ensures picking accuracy while still maintaining speed.
However, these systems work best for warehouses that store hundreds or thousands of individual SKUs. If your facility stores only a few different products, this kind of organization is overkill. Fewer product types mean you have less chance of a mispick and won’t receive the full benefit of solutions like vertical lift modules.
6. You Keep a Messy Facility
Despite automation’s incredible diversity, nearly all autonomous units require one thing: clean floors. Even units that can dynamically sense obstacles, like the Bastian Solutions ML2 AV, still need reliably debris-free floors. The more obstructions an autonomous vehicle encounters, the more often it has to stop, delaying or even halting its work until the obstruction is cleared.
If your warehouse floors are cluttered or routinely soiled, you likely don’t have the floor conditions necessary for automation to be an effective solution in your facility. That said, some custom solutions can work around certain types of debris like light dust or food processing. However, these machines are the exception, not the rule.
The Lilly Company Is Here For You
We're here for you whether or not warehouse automation is in your future. With over 100 years in business, our expertise spans both analog and automated material handling solutions. So, if you're still not sure what is best for your facility, let us help. Our team has the expertise to evaluate your business needs and make the most cost-effective recommendations that will serve your business for years to come. To learn more about automated and non-automated material handling solutions, contact us online; if you're still not sure if you're ready for automation, get our free automation tool kit and take the Warehouse Automation Readiness Quiz.
Arkansas - Jonesboro
Alabama - Birmingham, Dothan, Irondale, Madison, Mobile, and Montgomery
Mississippi - Belden, Tupelo and Richland
Tennessee - Jackson, Kingsport, Knoxville, and Memphis
Further Reading
AGVs 101: Your Guide To Autonomous Warehouse Vehicles
Product Review: T7AMR Robotic Floor Scrubber
Product Review: Toyota Core Tow Tractor Automated Forklift
Posts by Tag
- Forklift (61)
- Forklift Service (19)
- Electric Forklifts (15)
- Forklift Safety (15)
- Forklift Attachments (12)
- Product Review (12)
- Toyota Forklifts (12)
- Warehouse Automation (10)
- Warehouse Planning (10)
- Parts (9)
- Pallet Racking (8)
- Clark Forklifts (7)
- Loading Docks (7)
- Material Handling Education (7)
- Customer Solutions (6)
- Forklift Batteries (6)
- Forklift Rental (6)
- Purchasing Options (6)
- Aerial Equipment (5)
- Heavy Equipment (5)
- Forklift Accessories (4)
- Forklift Fleet Management (4)
- Forklift Tires (4)
- Forklift Training (4)
- Pallet Jacks (4)
- Products (4)
- Utility Vehicles (4)
- Yard Spotter Trucks (4)
- Linde (3)
- Specialty Forklifts (3)
- Used Equipment (3)
- Warehouse Doors (3)
- IC Forklifts (2)
- Manitou (2)
- COMBiLift (1)
- Custom Shop (1)
- Forklift Brakes (1)
- Forklift Warranty (1)
- Gehl (1)
- Komatsu (1)
- Recruitment (1)