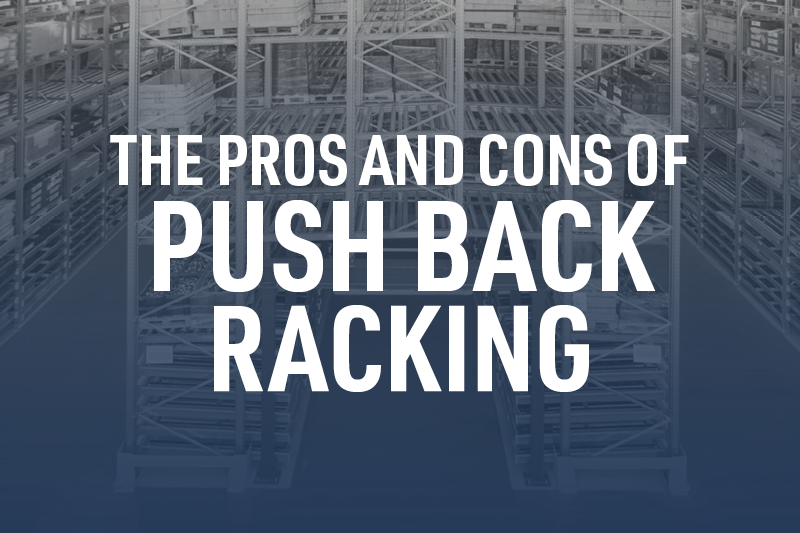
Today's warehouse management can feel like high-stakes Tetris. Each square foot of space must be optimized to avoid revenue loss. If that wasn't challenging enough, more and more warehouses are being asked to adapt to micro-fulfillment, forcing managers to strike a balance between inventory volume and SKU variety. That's why high-density racking systems are more critical than ever before.
There are many types of high-density racking systems, but a growing favorite is push back racking. This system dramatically improves storage density while keeping product selectivity high. However, push back pallet racking isn’t perfect for every application. Read on to learn the advantages and disadvantages of this versatile racking system.
Advantages
Push back racks offer a wide assortment of advantages for many warehouse applications. Below are the most common benefits of adopting this racking system.
Increased Storage Density
The most significant advantage of a push back pallet racking system is the increase in storage density. Each lane of each tier can hold 2 to 6 pallets. This means you use more of your warehouse space for storage and less for picking aisles. Push back racking can easily triple your storage density compared to selective pallet racking.
Faster Loading and unloading
With other high-density racking systems, such as drive-in racking, the forklift operator must drive into the lane to pick each pallet after the first. This slows productivity as the driver must travel farther and move with extra caution to avoid hitting the rack itself. However, push back racking uses gravity-fed rails to deliver pallets to the front of the rack automatically. This removes the need to drive into the lane and increases order fulfillment efficiency.
Reduce risk of racking damage
As mentioned above, other high-density racking systems force the operator to drive the forklift into the narrow racking lane. This confined space increases the likelihood of an impact between the forklift and the racking uprights. Such an impact damages your racking and products. In severe cases, it could even lead to a rack collapse and injury to the driver.
Improved product selectivity
The rail systems used in push back racking only occupy a single tier of each pallet rack, allowing the forklift operator to access each tier independently of the others. This independence between tiers allows different SKUs to be stored on each tier, allowing a wider variety of products to be stored compared to other high-density racking systems.
adaptable to product size
Another advantage of push back racking is its modularity. Its depth and height adaptability means it can be easily integrated with other racking systems, such as gravity flow pallet racking. This flexibility allows you to use a different racking system for each SKU as necessary to optimize your warehouse.
Disadvantages
No storage system is perfect, however. Even push back racks are not recommended for all applications. Below are the areas which do not lend themselves well to this racking system.
limited compatibility with perishable goods
By default, push back racking is a first-in, last-out system. This makes it a poor choice for highly perishable products or mildly perishable products with very low turnover. If your warehouse stores highly perishable products, you would benefit from a different type of pallet racking, such as a FIFO racking system.
specific storage depths
To optimize space, push back racking requires uniformity in depth for each rack on an aisle side. Push back racking comes in depths of 2 to 6 pallets, but storing items with mixed inventory volume on the same aisle can make the system less efficient. For example, if your push back racking is 4 pallets deep, using it to store 3 pallets of some SKUs and 2 pallets of others wastes space. This defeats the primary benefit of this system. For this reason, push back racking is generally recommended only for SKUs with an average inventory volume of 5 or more pallets.
where to learn more
Still unsure which combination of storage systems is best for your facility? We can help. Our experts can conduct a free site assessment to determine which racking systems are best for your needs. To learn more about high-density storage solutions, contact us online or visit one of our Mid-South locations:
Arkansas - Jonesboro
Alabama - Birmingham, Dothan, Irondale, Madison, Mobile, and Montgomery
Mississippi - Tupelo, and Richland
Tennessee - Jackson, Memphis, Knoxville, and Kingsport
Further Reading
Different Types of Pallet Racking
Used Pallet Racking: Is It Worth The Risk?
8 Expensive Warehouse Design Mistakes
Posts by Tag
- Forklift (61)
- Forklift Service (19)
- Electric Forklifts (16)
- Forklift Safety (14)
- Forklift Attachments (12)
- Toyota Forklifts (12)
- Warehouse Planning (10)
- Parts (9)
- Warehouse Automation (8)
- Clark Forklifts (7)
- Loading Docks (7)
- Material Handling Education (7)
- Pallet Racking (7)
- Customer Solutions (6)
- Forklift Batteries (6)
- Forklift Rental (6)
- Purchasing Options (6)
- Aerial Equipment (5)
- Heavy Equipment (5)
- Forklift Accessories (4)
- Forklift Fleet Management (4)
- Forklift Tires (4)
- Forklift Training (4)
- Products (4)
- Utility Vehicles (4)
- Yard Spotter Trucks (4)
- Linde (3)
- Pallet Jacks (3)
- Specialty Forklifts (3)
- Used Equipment (3)
- IC Forklifts (2)
- Manitou (2)
- Warehouse Doors (2)
- COMBiLift (1)
- Custom Shop (1)
- Forklift Brakes (1)
- Forklift Warranty (1)
- Gehl (1)
- Komatsu (1)
- Product Review (1)
- Recruitment (1)