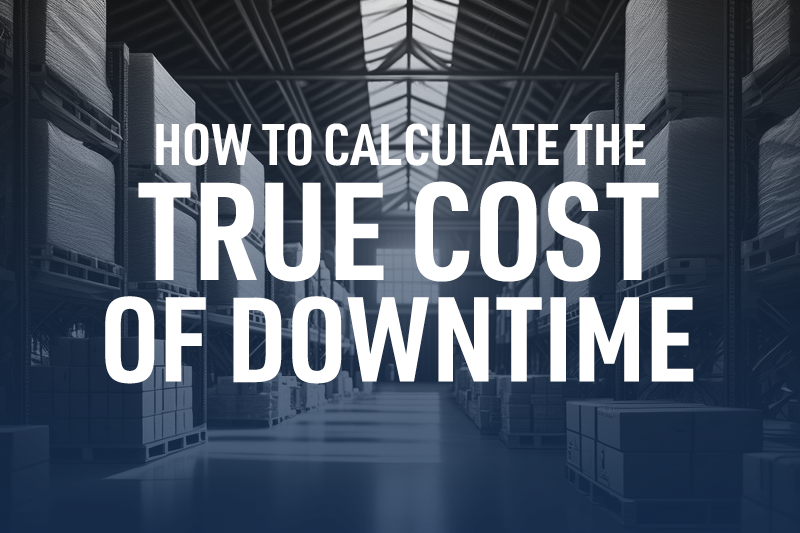
You've probably seen splashy dollar signs thrown around about the "real" cost of downtime. You might have even rolled your eyes. After all, you've had forklifts repaired. They cost a few thousand dollars and some lost time. Not great, but nothing to lose sleep over, right?
Not quite. Sure, the forklift repair might seem like small potatoes, but if you break your leg, the bone isn't the only part of the body that suffers. Your forklift is like that bone, but your warehouse is the body. The bone is the thing that needs fixing, but it affects every other part of the whole. Likewise, unplanned downtime affects your entire warehouse, costing much more than the repair. Read on to dig into the numbers and learn how to calculate the true cost of unplanned downtime.
Why Care About Downtime Costs at All
If you're like most warehouse managers, unplanned downtime triggers thoughts of repair bills and delays. Yet very few operations actually understand what unplanned downtime actually costs them. The actual cost of downtime is unique to each business, but here are some typical averages:
- Manufacturing: $20,000 - $22,000 per hour
- Warehousing: $10,000 per hour
- Food processing: $6,000 - $9,000 per hour
Downtime costs more than just a repair job. Unplanned downtime is a profit-killer that could cost you millions. Understanding the cost is the first step to preventing downtime.
How To Calculate Downtime Cost
The key to calculating downtime's actual cost:
- Identify every aspect of your process and workforce that experiences reduced productivity during unplanned downtime
- Quantify the lost dollars for each, and total the expense
First, we'll discuss a few common but often overlooked costs. Then, we'll walk through an example of how it all fits together.
Forklift Repair
Repair is the cost most associated with unplanned downtime. When calculating downtime expenses, add up the average price of parts and service for each forklift. Determine how long an average forklift repair takes and divide the cost by the duration to find the cost per hour for repair. If the forklift will be down for an extended period of time, you may also have to rent one so that your operation doesn’t grind to a complete halt.
Lost Productivity
Repair isn't the only cost of a downed forklift. There is also the expense of the work that isn't happening. For example, the forklift's operator’s time during the wait for the repairs. They can't do productive work during this time, yet they're still being paid. Likewise, the loading dock team might be idle during an emergency repair. Their wages are also a downtime cost. Determine all the staff affected by unexpected downtime and total their hourly wages.
Getting Back on Schedule
Unplanned downtime puts everything behind, and getting back on schedule also comes with a cost. One of these expenses is overtime for warehouse workers trying to pick up the slack. Similarly, your clients have their own deadlines and expect on-time delivery. You may now have to eat the cost of expedited shipping to meet that commitment. That, too, must be accounted for when calculating downtime.
Unseen Losses
All of the above are manageable if occurrences are few and far between. Yet, a failure to plan is a plan to fail, and if you fail to prevent downtime, it will recur. With each instance, company morale and reputation degrades. Clients lose their patience with late deliveries, and employees burn out. Soon, your organization is scrabbling to make up for revenue losses and trying to find the staff to keep up with the workload.
Downtime Adds Up
With the whole picture in mind, let's look at an example of this calculation. We'll use round numbers for simplicity's sake, but you should use your facility's actual costs when you do yours.
First, we identify all our expenses:
- Forklift repair. We'll assume an average repair bill of $5,000 and 8 hours of unplanned downtime annually, costing $625/hour.
- Lost productivity. The average forklift operator makes $22/hour in the U.S., and the average warehouse worker makes $16/hour. For this example, let’s say downtime affects one forklift operator and two warehouse staff, costing $54/hour.
- Playing catch-up. We lost 8 hours of work, which means we'll need 8 hours of overtime to make up for that. Let's assume overtime costs time-and-a-half, meaning our forklift operator makes $33/hour, and our warehouse workers make $24/hour each. That brings the total hourly rate to $81.
- Workforce Loss. Let's also say the added strain of these emergencies cost us one experienced member of our warehouse team. We now have to find, hire, and train a replacement. Bringing new staff on board often costs as much as three times that employee's annual salary. In this case, that makes the cost $33,280. Since 8 hours of unplanned downtime was the cause, we divide that number by 8 for a cost of $4,160/hour.
Now, let’s put it all together: $625 (forklift repair) + $54 (lost productivity) + $81 (overtime) + $4,160 (staffing) = $4,920 per hour of unplanned downtime.
Already, that number is almost eight times more than the cost of the repairs alone, and it assumes no expedited shipping or loss of customer loyalty. Moreover, the more forklifts you have, the more likely you will experience unplanned downtime. Old forklifts, in particular, are more prone to emergency repairs.
How To Prevent Downtime
Most unplanned downtime is 100% preventable with planned forklift maintenance. Preventative maintenance keeps your forklift running at peak performance all year, dramatically reducing the strain on your organization. Maintenance does create planned downtime periods, but planned downtime doesn't have the same chaos-inducing effects on your budget. It costs much less than an emergency repair, but it's also part of your plan, meaning it occurs on your schedule. That way, your workforce doesn't burn out trying to catch up, and your customers still receive all their orders on time.
At the end of the day, it's up to you to make the best financial choices you can for your organization. Do the math. Calculate what unplanned downtime really costs your organization, and then reach out for a quote on one of our forklift service plans. We're willing to bet the best choice becomes abundantly clear. To learn more about forklift maintenance plans or to request a quote, contact us online or visit one of our Mid-South locations:
Arkansas - Jonesboro
Alabama - Birmingham, Dothan, Irondale, Madison, Mobile, and Montgomery
Mississippi - Tupelo and Richland
Tennessee - Jackson, Memphis, Knoxville, and Kingsport
Further Reading
Should You Repair or Replace Your Old Forklift?
Fast Forklift Repair That’s Done Right
How Often Should a Forklift Be Serviced?
Posts by Tag
- Forklift (61)
- Forklift Service (19)
- Electric Forklifts (16)
- Forklift Safety (14)
- Forklift Attachments (12)
- Toyota Forklifts (12)
- Warehouse Planning (10)
- Parts (9)
- Warehouse Automation (8)
- Clark Forklifts (7)
- Loading Docks (7)
- Material Handling Education (7)
- Pallet Racking (7)
- Customer Solutions (6)
- Forklift Batteries (6)
- Forklift Rental (6)
- Purchasing Options (6)
- Aerial Equipment (5)
- Heavy Equipment (5)
- Forklift Accessories (4)
- Forklift Fleet Management (4)
- Forklift Tires (4)
- Forklift Training (4)
- Products (4)
- Utility Vehicles (4)
- Yard Spotter Trucks (4)
- Linde (3)
- Pallet Jacks (3)
- Specialty Forklifts (3)
- Used Equipment (3)
- IC Forklifts (2)
- Manitou (2)
- Warehouse Doors (2)
- COMBiLift (1)
- Custom Shop (1)
- Forklift Brakes (1)
- Forklift Warranty (1)
- Gehl (1)
- Komatsu (1)
- Product Review (1)
- Recruitment (1)